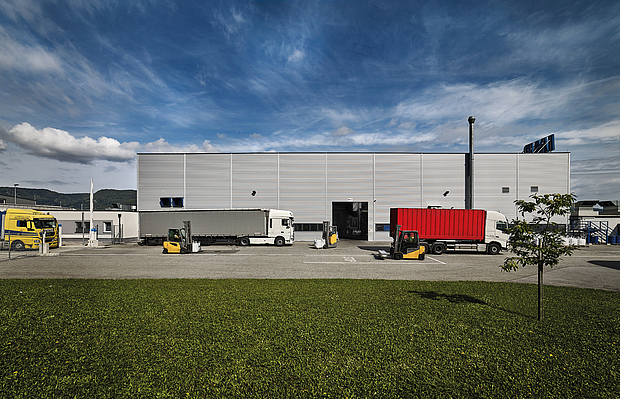
We don’t just practise sustainability today, we already practised it in the past. Co-products from our production, such as dust, dross and hard zinc, are returned to the secondary raw material cycle in the interests of sustainable utilisation and are thus given a new life cycle, which is why we see ourselves as an integrally active company that is active in all levels of recyclable materials and makes the circular economy an integral part of its strategy.
We prioritise CO2-reduced precursors to reduce our own CO2 footprint and pre-select the raw materials to be used in advance from our suppliers. We can already report the CO2-equivalent share on the basis of our certificates.
When it comes to transport, we prioritise rail and intermodal transport, depending on transport logistics feasibility. We aim to harmonise environmentally friendly transport and on-time delivery.
Our smelting plant, where we produce metal anodes, metal powders and alloys, only uses electricity to manufacture all of our products, and we are also able to break down the individual types of electricity, such as hydroelectric power, wind power and solar power, on the basis of the certificates.
It is especially important in the raw materials industry to not just think green, but also to act accordingly. This underlying principle is our top priority when it comes to sustainable management,